Hobhouse
Protecting history, redeveloping on a delicate footprint and setting a new sustainability benchmark. All at once.
Project Details
AIA Miami, Merit Award, 2021
UK Institution of Structural Engineers, Sustainable Leadership Award, 2020
AIA Florida/Caribbean, Merit Award, 2020
The Challenge
In the heart of Central London, Hobhouse lies amid such celebrated landmarks as Trafalgar Square and the National Gallery. Creation of this 7,000-square-metre mixed-use development in such a dense and compact historic area required a highly technical balancing act that entailed refurbishing, restoring and redeveloping buildings along Whitcomb Street; creating new basement areas; building new structures; realigning the streetscape; and creating new public spaces. The project also included restoration and redevelopment of a Grade II-listed building designed by renowned Georgian architect John Nash, along with preservation of its 200-year-old subterranean masonry vaults.
Here's How
A Digital-First Mindset
Our engineers relied on a few valuable digital tools to help the team make informed decisions and keep the project on track:
- We used a 3D model to help visualise the complex geometries of the new and existing buildings, as well as Rhino models from the architect and our own Grasshopper scripts, for laying out and coordinating the columns with the inclined façade.
- The survey company translated the existing structures into a 3D environment to illustrate how key new structure interfaces with the existing structure.
- Autodesk BIM 360 enabled us to work with data in real time to ensure coordination against the latest information.
- We relied heavily on Konstru, which enabled data synchronisation between building design and analysis applications without requiring reworking.
Ease of Constructability in a Complex Footprint
Achieving the client’s aspirations of differing building uses, maximum lettable area and clear span floor plates whilst staying within the remits of the listed structures presented a significant technical challenge and potential risk to the project. Close collaboration with the project team early in the design process was essential to understand the constraints and limitations on what could be achieved.
We used a detailed series of surveys and testing programmes to understand the condition and capacity of the retained building and vaults so we could develop the design accordingly. The ability to retain and reuse existing structures vastly decreased the demand for materials, cost and amount of time required for the construction of an all-new development. The project team estimates savings at approximately 1,100 cubic metres of additional demolition spoil and the construction of approximately 900 cubic metres of new reinforced-concrete basement.
Construction of the new development had to be carefully balanced against the existing vault structure to minimise structural interventions and preserve its heritage. The client’s desire for clear span plates for the new floors above the vault required loads to be concentrated into a limited number of locations, a condition not suitable for masonry construction. The solution: a ground-floor transfer grillage that evenly spreads the weight of the building over the vaults. To preserve the historic nature of the basement area, no new columns or foundations – except for the new lift pits – were constructed through or within it.
Structural zones to the floors and walls were minimised, not only to limit storey heights and maximise internal spaces, but also to minimise the amount of required material. A slim floor system that fit within the structural slab depth using fabricated shallow beams and “plug composite action” enabled a very compact structural zone and clear spans of up to 9.5 metres, meeting the market demand for open areas with substantial floor-to-ceiling heights.
The façade for the new-build elements features handset bricks and punched windows. As the building rises, the brick cladding transforms into a faceted shape with many angles, minimising the massing on the streetscape and allowing pedestrians to see more of the sky. Using prefabricated, structurally insulated panels as the inner leaf contributed not only to the load-carrying system for the faceted handset brick façade but also its thermal performance.
A New Benchmark for Low Embodied Carbon Buildings
The design team and client agreed to the goal of developing a low-embodied-carbon building by combining material retention with efficient design:
- The new building’s external wall buildup, which consisted of prefabricated lightweight insulated panels to minimise the number of required material layers, helped reduce the embodied-carbon total.
- Retaining and reusing the existing building and vaults vastly decreased the demand for new construction materials.
- The concrete replacement material from the recycled demolition spoil contained 60 to 80 percent ground granulated blast-furnace slag, similar to fly ash.
Our carbon calculator has measured the embodied carbon of the building’s structural elements as 375kgCO2e/sm and the overall building figure at 495kgCO2e/ sm. The building’s embodied carbon fell below the London Energy Transformation Initiative’s (LETI) proposed 2020 targets, even though we conceived its design much earlier, in 2013. The project also pursued BREEAM green building certification and achieved a rating of “Excellent,” receiving all six available credits for embodied-carbon reduction.
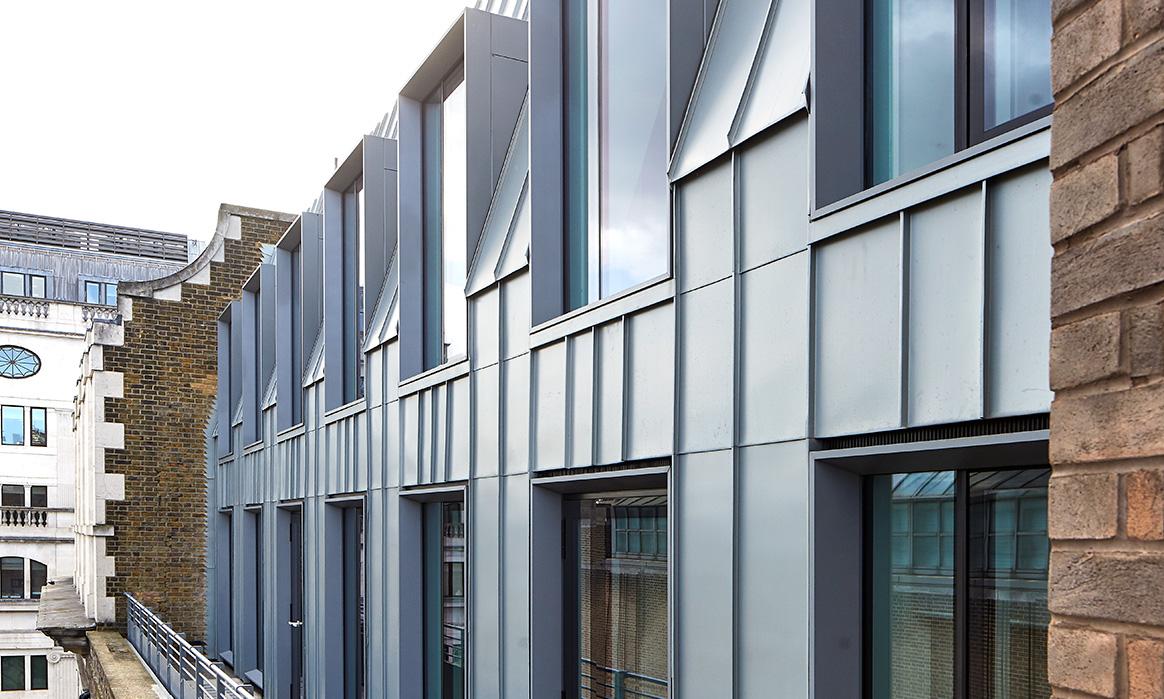
Results
Hobhouse is a prime example of how existing buildings can be creatively reinvented, regenerated or repurposed using a mixture of technologies to create an expressive and efficient development.
The new buildings have made a positive economic and social contribution to the historic area while the retention and reuse of the existing structures have allowed these “lost” spaces to be reopened to the public for gallery and retail use. The creation of new public spaces and the realigned streetscape has rejuvenated the area. Among the many project successes was the return of the Royal Watercolour Society – who previously occupied the building for 115 years – to its original base once the development reopened.