Willis Tower Repositioning
Expanding the retail and guest experience at one of Chicago's most popular tourist destinations.
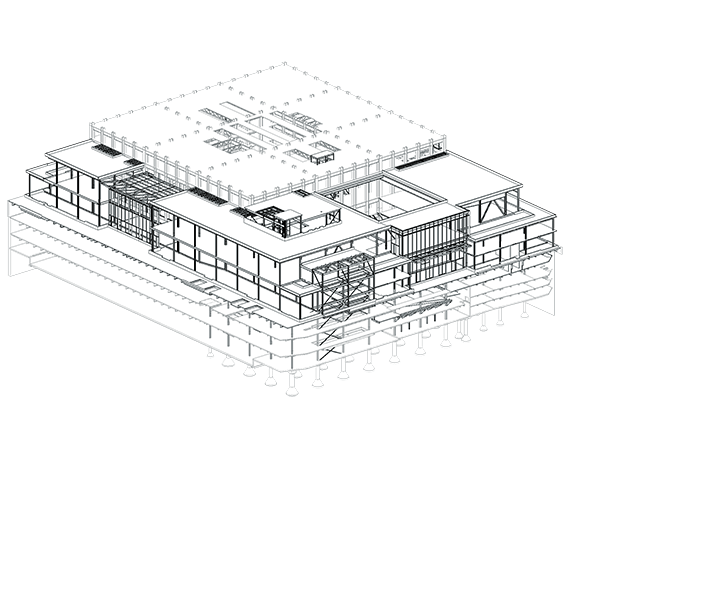
Project Details
AIA Chicago, Design Excellence Awards – Interior Architecture Honor Award (Large Projects), 2022
Retrofit Magazine, Metamorphosis Awards - Mixed Use, 2022
Architizer, Popular Choice Award, 2022
Chicago Commercial Real Estate Award, Redevelopment of the Year – Office/Retail, 2021
SEAOI, Excellence in Structural Engineering Award – Renovation/Rehabilitation, 2020
the challenge
The 110-story Willis Tower (previously known as the Sears Tower) was completed in 1974 becoming the tallest building in the world – a title it held for nearly 25 years. This renovation provided Willis Tower with a massive "base-lift" to expand the retail and tourist experience at the building’s first six levels. The existing plaza was replaced with a three-story retail structure featuring a winter garden with a grid shell skylight; 300,000 square feet of new retail, dining and entertainment; a belowground entrance to the Skydeck; and a rooftop green space that is open to the public. Thornton Tomasetti integrated structural engineering, façade engineering, construction engineering and protective design services helped realize the owner's vision for this iconic tower.
But making significant changes to a building that has stood for more than 50 years brings unique challenges. First and foremost, the tower needed to remain open and in operation throughout construction. And how do you construct a new three-story podium and distribute the load from above down to the existing superstructure without adding any new foundations?
Here's How
Bringing the Architectural Vision to Life
The architect designed the podium's column grid to match the 15-foot module of the Tower. However, the belled caisson foundations of the existing podium have an irregular layout with varying capacities. To distribute the load from the current to the existing column grids, we designed 72 transfer columns and approximately 80 transfer girders. Several of the transfer beams supporting the new columns are W40x503 sections – the heaviest steel shapes available in the United States.
This was an iterative process and required close coordination with the architect. To filter through the architectural and structural data, our engineers developed tools that allowed us to clearly see which caissons were near capacity, which were at capacity, and which could be used to distribute more load. The ability to filter and sort this information quickly and accurately was critical, because while the information might change from week to week or even day to day, we always needed to know that the load was distributed properly.
This strategy allowed us to optimize a design requiring no new foundations.
Rehabilitating Building Components to Support New Podium
Most of the lower-level plaza columns outside of a planned, but unbuilt, hotel footprint could not support more than one additional floor. Our engineers determined that 20 columns required strengthening to support the vertical addition. We encased the existing steel wide-flange columns in concrete and welded headed studs to the column webs, which spread the load between the steel section and the concrete encasement. Where existing site constraints prohibited concrete encasement, we designed partial-height plates welded to the existing column flanges to add the necessary strength.
We worked with Terracon, the geotechnical engineer, to determine if the soil around the existing foundations could provide a higher bearing capacity. By employing various strategies, including drilling through existing caissons and performing in-situ soil tests, we determined that the soil compacted by the existing building over the past 40+ years provided the increased bearing capacity that we needed to support the new podium structure.
Relocated Tower Spandrel Beams
The architect wanted a new stair connecting the street level to the second level, but the proposed design conflicted with three 42-inch-deep spandrel beams. To accommodate the stair, we needed to lower the spandrel beams by three feet. We developed a 3D model of the tower to analyze the increase in force on the surrounding columns and girders and used the results to develop reinforcing details to locally increase their strength the stiffness. We also provided sequencing for the demolition and replacement of the spandrel beams.
Putting A New Face on a Classic
The new three-story podium features seven different façade systems and a complex gridshell skylight. The primary skin systems are composed of custom steel and aluminum glazing and stainless steel metal plates.
We took a high-tech approach for a new 75-foot by 90-foot skylight over the new "Catalog" atrium. We rationalized its form into a logical and economical design comprising a doubly-curved shell with planar glass panels. We then coordinated with Novum Structures, a specialty contractor that was brought on at 95% design development to carry out the final design and detailing. The design consisted of an AESS Category 2 stick-built system using high-strength bolted moment connections at each node. Access holes on the top faces of the steel tubes allowed the tension bolts to remain hidden and eventually be covered by the glazing.
Our façade experts provided detailing for the façade systems, specialty glass selection, and specification review. We also performed shop drawing and product data review, site and plant visits, and field test witnessing during construction.
Designed with Safety in Mind
More than 300 steel pipe bollards stand sentry around the new podium, designed to protect pedestrians and building occupants from accidental or intentional vehicle impacts. Their simple appearance above grade is akin to an iceberg above the surface. But below the sidewalks, reinforced concrete grade beams support the bollards. Dense urban environments like Chicago have myriad existing below-grade structures that constrain and conflict with these footings. We customized the footings to squeeze past high-voltage equipment rooms, avoid fire hydrants, span over manholes, skim the edges of tree planters, and retain maintenance access – all while marching in an orderly line down each block. Along the Wacker Drive viaduct, we integrated the bollard footings with the building's elevated structural slab.
From Start to Finish
Our job isn’t done when the design is ready to go. Our Construction Engineering team provided structural engineering expertise to assist the general contractor, a joint venture between Turner Construction Company and Clayco, in detailing and sequencing renovations. From connection design to temporary shoring and bracing designs, our construction engineers were involved every step of the way. In addition to connections, we also designed temporary supports for the building as it underwent selective demolition tasks, which included slurry wall brace design, temporary column bracing, temporary support of utility pipes, review of crane and equipment loads, and construction and demolition sequencing.
Results
By adequately addressing and respecting existing conditions, the design and construction team set the stage for creating the elements that would make a half-century-old building seem new again. Through steel technology and, more importantly, collaboration and creative thinking across the project team, this update provides a new appreciation for—and a new way to enjoy—this landmark tower.