Protecting the Gina Krog Offshore Production Platform
The Gina Krog offshore production platform is supported by a structure of 17,000 tons, more than twice the weight of the Eiffel Tower. How do you protect a $4.1-billion investment from diverse risks?
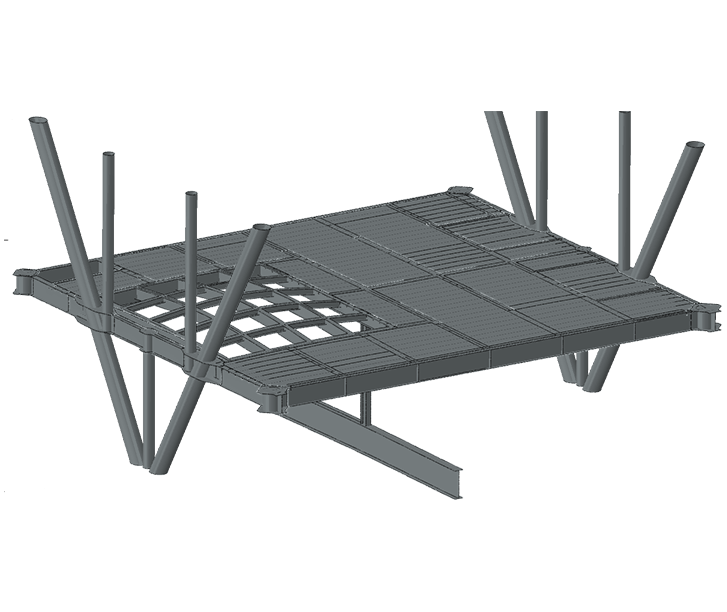
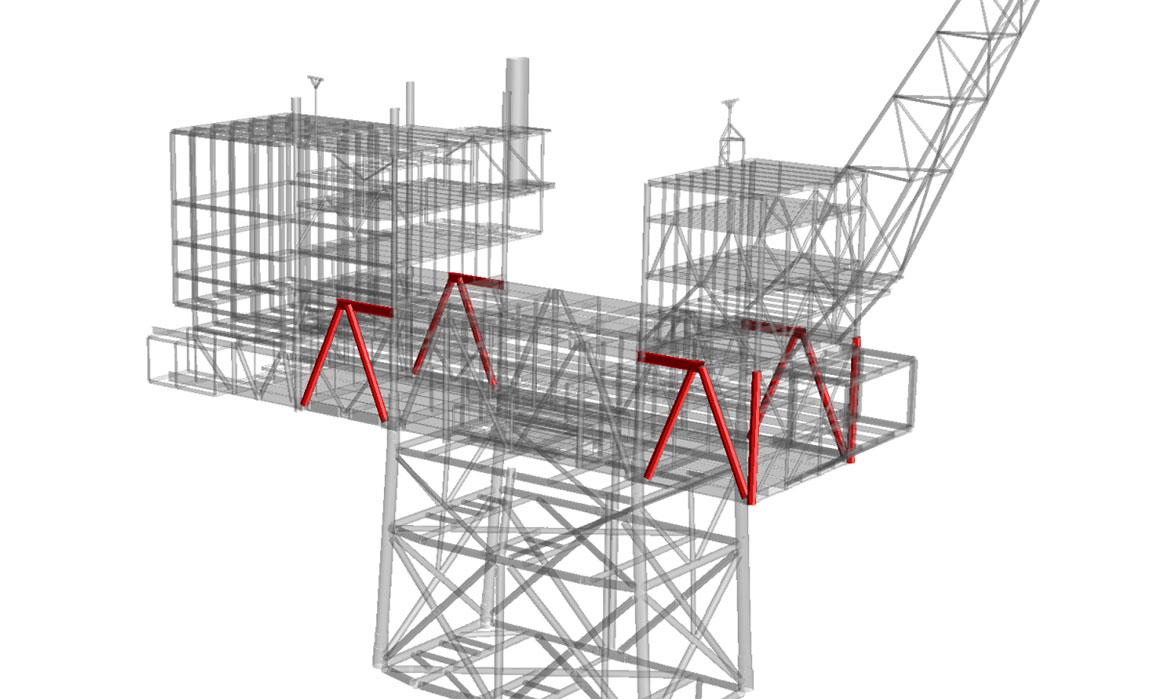
The Challenge
In 2013, during the early design phase of the offshore production platform, we were asked to provide a wide range of analyses to determine the safety of the structural design and ensure the platform met Norway’s safety standards. Our goal was to ensure the resilience of the topsides structures to preserve the safety of personnel for a range of extreme accidents. Our recommendations were implemented in time for the platform to come on stream in 2017, one year after the centennial of the death of the field’s namesake, Gina Krog, the suffragist and leader of the Norwegian women's movement.
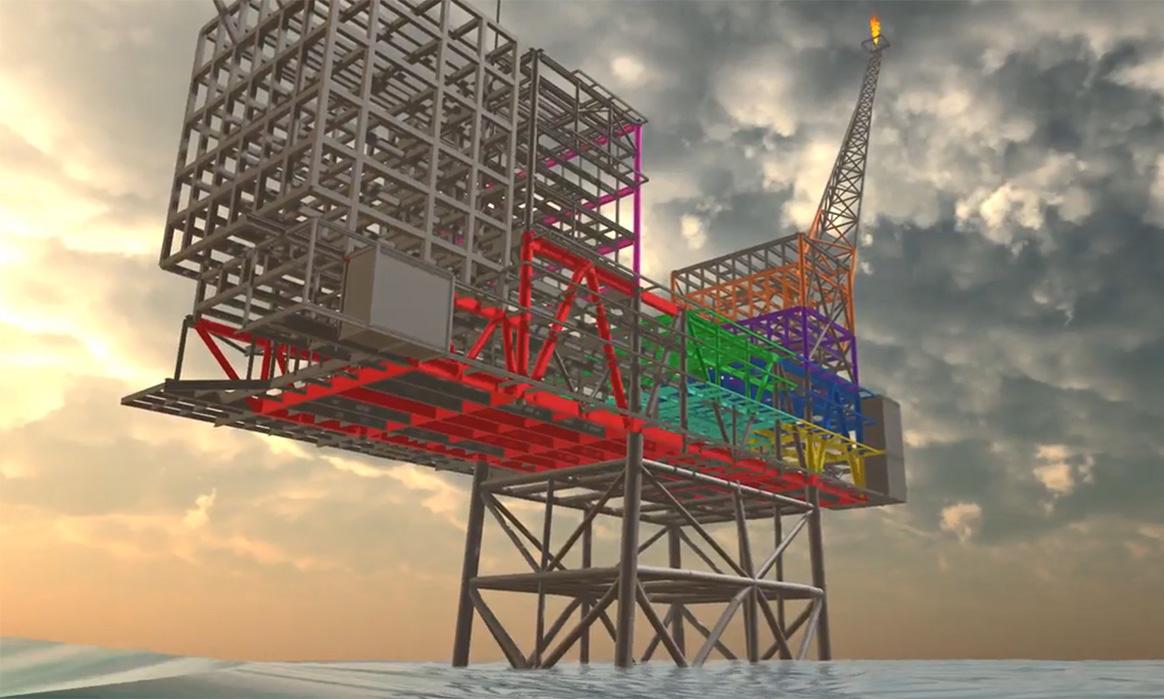
Here's How
Mitigating Diverse Risks
We conducted performance-based fire analysis and optimisation of passive fire protection (PFP), blast analysis of structure and blast walls, dropped-object impact analysis, ship impact analysis, and computational fluid dynamic (CFD) analysis of the wind-tunnel effect between Gina Krog and the adjacent Maersk Integrator, a floating jack-up rig. Where we found a problem, we provided a design solution to improve the response of the platform.
Our fire analysis and PFP design aimed at the prevention of fire escalation due to local failure of vulnerable structures, ultimately preventing the global collapse of the platform. To determine if the structure met relevant acceptance criteria, we considered the thermal loading in each fire zone of the topside by importing the CFD results from the fire spread analysis, and sought to capture the nonlinear structural response of the structure to the effects of fire. The primary criterion for acceptance was the preservation of integrity for the topside structure for the period required for people to safely evacuate.
Our blast analysis consisted of a range of assessments to examine the local and global response of primary and secondary structures subjected to explosion loading. Dynamic analyses were conducted to understand the global response of topsides primary structure, as well as the decks and bulkheads. We generated more detailed finite-element models to assess member stability and to study local buckling responses using implicit and explicit dynamic analysis methods.
The dropped-object impact analysis considered the dynamic response of the structure to a dropped object falling onto different areas of the structure. This study sought to minimise localised failures of critical structural elements and investigate any failures that could jeopardise the global integrity of the structure.
We performed ship impact analyses for multiple locations, impact types and energies. Static ship impact analyses allowed us to assess the post-impact structural capacity of the damaged structure. Dynamic ship impact analysis was undertaken to ensure that the static analysis did not underestimate the structural dynamic response of the topsides as well as to identify accelerations in the topside.
Maesrk Integrator is jacked into place, supported on three legs and connected by a bridge to Gina Krog during drilling. The wind loading of the bridge needed to be established to enable appropriate structural checks. Our CFD study assessed the wind speed factor required for the subsequent structural checks of the bridge. The objective of the work was to assess the localized increase in wind speed between the platform and MIG.
Results
Based on our analyses, we made recommendations for risk reduction and design revisions.
Fire Engineering
Our PFP scheme prevents the escalation of fire due to localised structural failure, failure of critical equipment such as flare booms, as well as preventing the global collapse of the platform. We optimized PFP coverage area and fire rating.
Explosion Analysis
Our analyses showed that enough margin is available between the specified design accidental loads and the capacity of the topsides structural barriers to resist them.
Dropped Object Impact Analysis
Based on a combination of global and local analyses, we determined that damage to topside structures caused by dropped objects required strengthening of certain structures. To address this, we redesigned several structures including deck hatches, pipe supports of high-pressure gas lines, and added drop protection barriers for cable and deck protections.
Wind Tunnel Effect
Our CFD analysis identified the expected wind velocities and pressures on the bridge connecting the platform with the support vessel. This information was used to design the bridge and its connections. The results showed that the design guidance from the applicable standards could be relaxed, providing a cost -effective bridge solution.